The increasing focus on sustainable industrial practices has led many pump manufacturers to develop electric pumps to replace traditional pneumatic and hydraulic systems in fluid transfer applications. Compared to their pneumatic and hydraulic counterparts, electric pumps use energy-efficient technologies that reduce power consumption and minimise carbon footprints. Modern electric pumps are also designed to be more durable, requiring less maintenance and producing less waste. These improvements significantly lower the total cost of ownership while supporting environmentally friendly operations.
With these advantages, how much can electric pumps actually reduce costs and waste? A Graco case study compares the energy usage of an electric diaphragm pump with that of an air-operated double diaphragm pump, offering valuable insight into the potential savings for manufacturing plants.
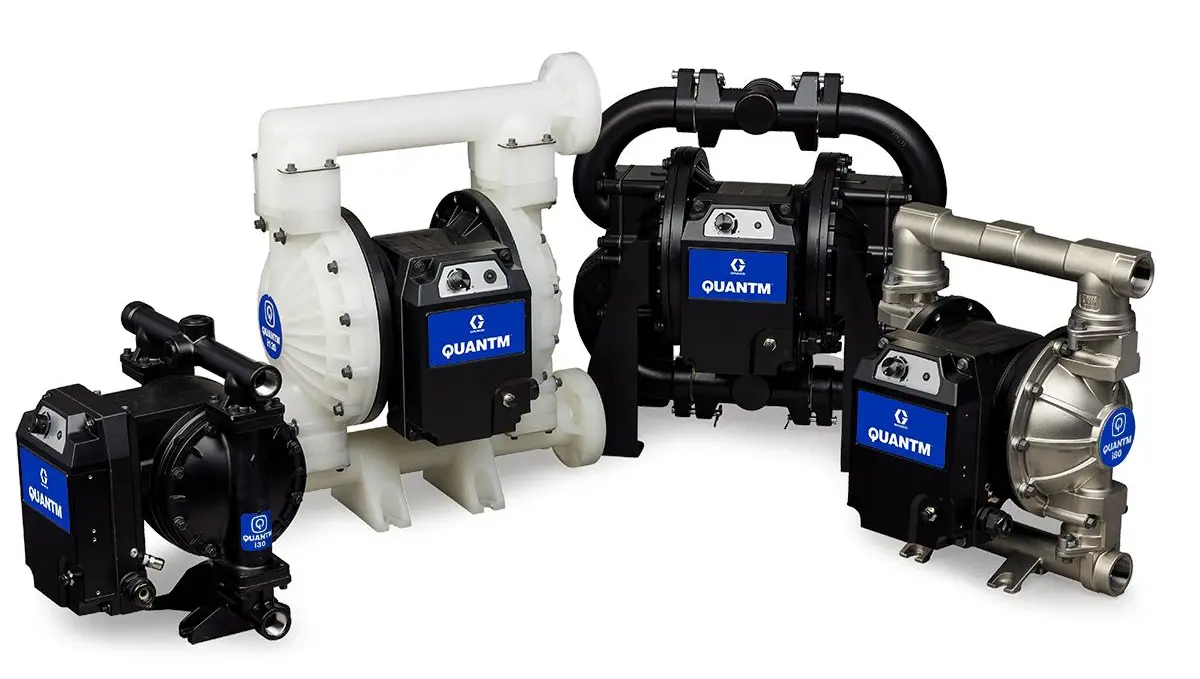
UK CORRUGATED CARDBOARD MANUFACTURER SHIFTS TO EODD PUMPS
A project led by a Graco distributor in the UK helped a corrugated cardboard manufacturer save nearly €1,000,000 (over 1.6 million AUD) annually after switching from AODD pumps to QUANTM electric glue pumps.
Initially, the distributor replaced two AODD pumps at the client’s factory with two equivalent QUANTM pumps. After running the pumps for a while, the manufacturer noticed a significant reduction in operating costs and saw the potential for further savings, prompting them to explore additional possibilities.
Following the successful installation, the distributor expanded its efforts to two other factories of the same client. They conducted a thorough 6-month testing period for two additional QUANTM electric pumps, which were responsible for transferring and circulating glue around the clock. This extensive testing yielded the following results in terms of energy consumption and costs:
2” QUANTM electric glue pump | 2” Air-operated double diaphragm pump | |
---|---|---|
Hourly average energy consumption | Between 928 and 995 watts = average of 961.5 watts/hrs |
Between 45 and 60 SCFM = average of 961.5 watts/hrs = average of 52.5 SCFM = 1.49 m³/min = 89.4 m³/hr |
The energy consumption was calculated on a yearly basis or 51 weeks, giving the annual average energy consumption of both pumps as follows:
2” QUANTM electric glue pump | 2” Air-operated double diaphragm pump | |
---|---|---|
Yearly average energy consumption | 24 hours x 7 days x 51 weeks x 961.5 watts /1000 = 8238 kWh per year |
24 hours x 7 days x 51 weeks x 89.4 m³/hr = 765,979 m³ per year |
With the average energy consumption, and assuming the energy price is £0.21 per kWh in the UK, and the production of 1m³ of air consumes 0.1339 kWh, the annual energy costs for each pump are as follows:
2” QUANTM electric glue pump | 2” Air-operated double diaphragm pump | |
---|---|---|
Yearly energy costs | 8238 kWh per year x 0.21 £/kWh = £1730 ($3,363.23 AUD) |
765,979 x 0.1139 kWh x 0.21 £/kWh = £18,321 ($35,617.40 AUD) |
The data reveals a significant difference of AUD 32,254.17 in annual energy costs, representing an impressive 91% savings. This clearly highlights the potential cost reductions that can be achieved by switching to QUANTM pumps.
After seeing the promising testing results, the client made the bold decision to replace nearly 115 pneumatic pumps with QUANTM electric glue pumps across their 12 factories, choosing a mix of 2” i120 Polypropylene/Santoprene and 1.5” i80 Polypropylene/Santoprene models. This successful transition resulted in an impressive €1,000,000 in annual savings, with a return on investment (ROI) achieved in just 5 months.
The client also highlighted that the QUANTM electric pumps play a key role in reducing carbon emissions, helping them meet the targets set by the Net Zero Standard and align with their sustainability goals.
2” QUANTM CO² emissions | 2” AODD CO² emissions |
---|---|
2.5 tons CO²/year | 11 tons CO²/year |
“Corrugated Cardboard manufacturers, if you are looking for ways to lower your energy bill: don’t leave your glue pumps out of the picture. It could be worth your while to include them in your electrification strategy.”
PUMPS IN GLUE TRANSFER APPLICATION IN CORRUGATED CARDBOARD MANUFACTURING
Glue is a crucial component in the production of corrugated cardboard, as it binds the layers of paper to create strong boxes. Pumps play an essential role in this process, transferring glue to the single facer and the glue application machine, also known as the gluer machine. They are also key in circulating glue throughout various stages of the manufacturing process.
Glue Transfer
In the early stages of production, glue is prepared in the glue kitchen and stored in a buffer tank. A pump is needed to transfer the glue from the main storage container into individual buckets placed next to the single or double-facer glue pans. The glue roll collects the glue and delivers it to the medium tips, while the metering roll ensures a consistent glue thickness, maintaining an even application of adhesive to each tip.
Starch Glue Circulation
Glue is continuously circulated between the buffer tank and the glue pans to prevent settling. A dedicated pump transfers glue from the glue pans back to the buffer tank. Any leftover glue collects in a tray beneath the gluer machine, where a third pump is installed to transfer the excess glue into a storage bucket for recycling and reuse.
At the end of operations, all glue in the corrugated line unit is pumped back into the main storage tank, ensuring it is ready for use the next workday. In summary, a minimum of three pumps is required for a basic cardboard manufacturing line.
GOING ELECTRIC IN GLUE TRANSFER
Pumping starch glue can be challenging, but with a solid understanding of its fundamental properties, efficient pumping is achievable.
- Abrasiveness: Some glues contain fine particles that can wear down the internal components of a pump, potentially causing breakdowns.
- Corrosiveness: Some glues may react chemically with the materials used in the pump's construction, resulting in internal corrosion.
- Shear Sensitivity: Many glues are sensitive to shear forces, meaning their properties can degrade during the pumping process due to the shear generated by the pump.
- Viscosity: Viscosity is a key factor when selecting a pump for glue applications. Glues can vary widely in viscosity, and highly viscous glues can affect the pump's performance and output.
- Temperature: Certain pumps can increase the temperature of the glue while in operation; however, electrically operated double-diaphragm pumps do not produce this effect. Generally, glue should not reach temperatures beyond 43.3°C (110°F), as it may start to gel.
- Flow: To ensure efficient glue transfer and application, it is essential to identify the minimum and maximum flow rates first.
While these glue properties can cause issues for many pumps, they are not a problem for electric pumps like the QUANTM. Graco has specifically engineered these electric diaphragm pumps to handle even the most challenging glues effectively.
The QUANTM electric pump stands out for its unique features that make it the perfect solution for glue transfer. These include:
- Does not shear glue: EODD pumps are gentle on the product and won't separate or alter it, thus preserving product integrity.
Handles a wide range of viscosities: QUANTM pumps are highly tolerant to changing glue viscosity. They can continue to deliver constant and consistent flow regardless of back pressure. - Does not heat the glue: EODD pumps do not heat the glue like other pumping technologies, which is a critical advantage since high temperatures can cause the glue to turn into a gel.
- Stalls under pressure: QUANTM pumps can stall under pressure, preventing pump failures due to clogged lines or closed valves.
- No mechanical seals: The absence of mechanical seals in QUANTM pumps means less expensive wear parts and lower risks of failure due to run-dry conditions.
- Simple design: The simple design and fewer parts of an EODD pump means easier cleaning and faster maintenance. All of these translate into reduced downtime and lower maintenance costs.
- Minimised energy consumption: The QUANTM pump features an energy-efficient motor that significantly reduces electricity consumption, offering potential energy savings of up to 80%.
- Simple control: QUANTM is much easier to control with its integrated I/O port for remote operation. This is a major advantage for metering and batching operations in glue manufacturing.
- Reliable pump solution: QUANTM pumps are reliable for continuous operation. Their robust construction and ability to handle abrasive fluids, such as certain glues, make them an ideal choice for 24/7 operation.
ABOUT QUANTM ELECTRIC-OPERATED DOUBLE DIAPHRAGM PUMPS
QUANTM electric diaphragm pumps are designed to meet the increasing demand for clean energy and sustainable solutions, while providing significant cost savings. They are not only perfect for glue transfer in corrugated cardboard manufacturing but also suitable for a wide range of applications across various industries, offering the following features:
- Using an advanced Fluxcore motor, QUANTM drastically reduces electrical losses, thus increasing efficiency and reliability.
- The simple one-touch knob and LED indicator with system status and onboard diagnostics allow easy adjustment of pump speed and pressure according to specific application requirements.
- QUANTM pumps are available in a wide operating range and materials to handle various media.
- QUANTM pumps are similar in size to existing AODD pumps, making replacement or new installation easy.
- QUANTM operates quietly at less than 75 dB, thus reducing plant noise and improving employee safety and health.
All-Pumps provides an extensive selection of Graco’s innovative QUANTM EODD pumps. This selection includes various configurations designed to deliver effective pumping solutions for challenges such as abrasion resistance, different types of glues, and a variety of cleaning agents, including water, soda, and other substances.