Overview
A repeat and loyal customer contacted us to order helical rotor pumps for use in their water treatment process. Several centrifugal pumps were also needed in their newly set up refinery application. After our thorough selection process, all pumps were delivered to their mining site in the North Territory.
The customer is in the process of building a tricanter centrifuge system to treat HFO wash waters. The application requires various pumps for the water treatment phase, where the system will extract oil and particles and clean the water for reuse.
Their engineering team pre-selected pumps that could satisfy the transfer duty conditions and sent us the piping and instrumentation diagram (P&ID). Our task was to check the P&ID and to size and supply the pumps suitable for the application. Value-added services included the fabrication of the pumps’ baseplates and the supply of variable speed drives and control panels to optimise efficiency and safety.
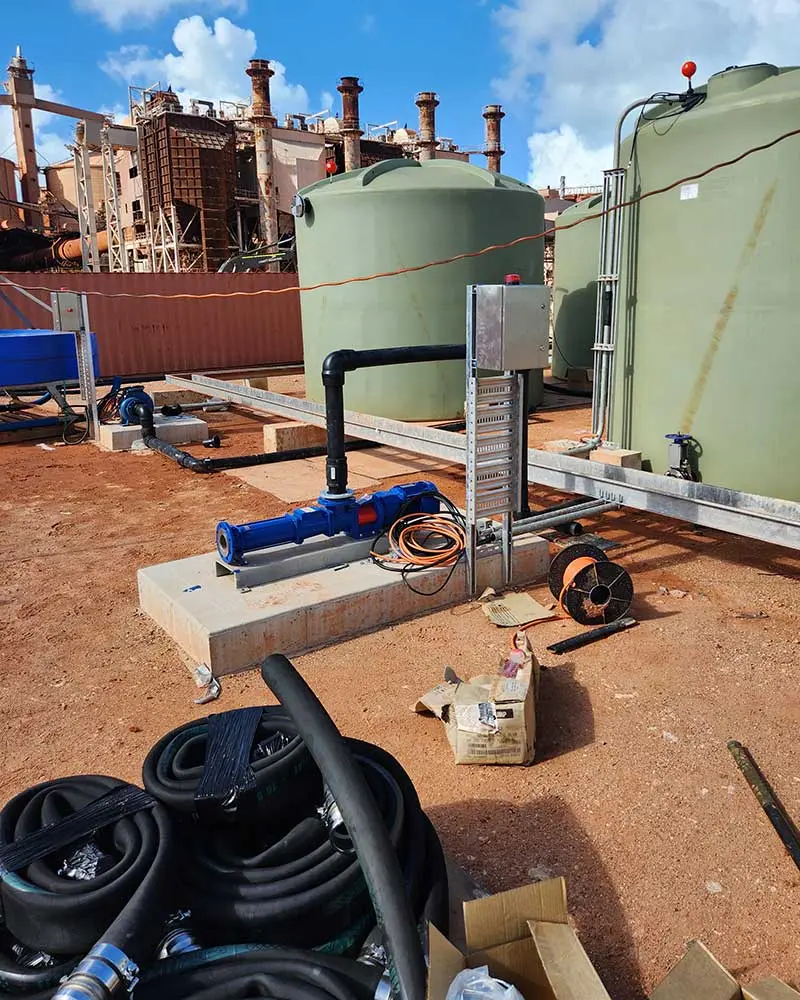
The Problem
Our team had to size and select the correct water treatment pumps for transferring various fluids with different viscosities and pressure ranges, including acids, sludges, slurries and oils.
The Solution
All-Pumps chose Nexus helical rotor pumps (AKA progressive cavity pumps) for the water treatment phase. The project also included other pumps, such as vertical multistage pumps functioning as the application’s decontamination pump that feed cleaning heads to the system. Horizontal centrifugal pumps were also used for pumping oil and chemicals in Zone 2-certified areas of the mines.
Project Highlights and Results
Nexus Helical Rotor Pumps for Water Treatment Process
Helical rotor pumps are widely used in water treatment processes. Self-priming and valveless, they can move sludge and other difficult fluids like solids, abrasives, and chemicals at high pressures and viscosities – making them the most suitable water treatment pumps for this refinery project.
Helical rotor pumps do not disappoint when it comes to performance. They can withstand temperatures up to 150 °C, have high discharge pressures up to 48 bar and capacities up to 345 m3/hr, and are designed for solid handling up to 7% without clogging and viscosities up to 30,000 cst.
Pumps Fitted and Mounted on Galvanised Baseplates
Pumps for this project were assembled on galvanised baseplates for uninterrupted and reliable service even when exposed to the harsh mining environment. Galvanised steel baseplates are used for corrosion protection that can last for decades. This technique is known as the toughest coating that provides outstanding resistance to mechanical damage. Galvanising of steel baseplates is done according to the Australian/New Zealand Standard 4680 (AS/NZS 4680-2006) to ensure reliable coating life and performance.
Variable Speed Drives and Pump Control Panels
In this application where variable flow and pressure are required, a variable speed drive (VSD) is needed to reduce power during periods of reduced demand. A VSD is one of the most efficient flow control methods for pumps and does not waste shaft input energy.
Variable speed drives adjust flow or pressure to the actual demand by controlling the frequency of the electrical power supplied to pumps. As a result, significant power savings can be achieved, and in most cases, improved performance, increased reliability, and reduced life cycle costs are also expected.
We also supplied control panels alongside pumps and VSD. The explosion-proof panels were customised to provide a centralised location from which operators can monitor and adjust the full range of pump process variables. This not only simplifies the control process of the pumps but also enhances safety for both the operators and the pumps.
Our longstanding relationships with world-famous pump manufacturers allow us to ship all pumps and accessories that our customers need.